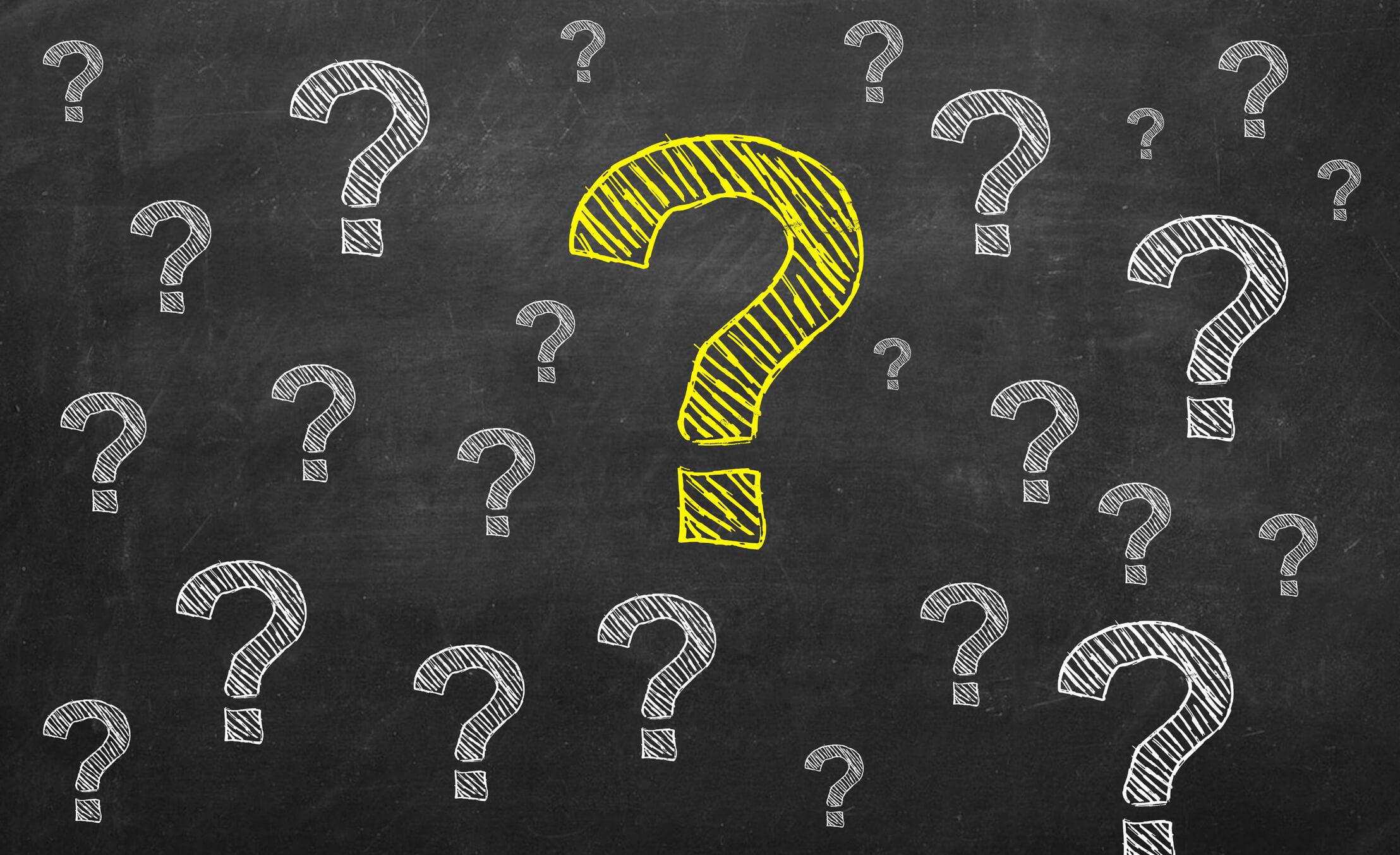
Everyone knows that investing in a robust software product like a fuel management system is nothing short of a big deal. It can be expensive. It’s critical to the functionality of your organization. And it can create countless problems, including in your finances, if the system chosen doesn’t run smoothly and report information accurately.
When given the OK to buy, it’s a good idea to start the process by asking the right questions up front. Whether talking to a sales representative about the fuel system or speaking with other organizations for tips and tricks, doing your research can result in monumental benefits. While it takes time to truly understand the key differences between fuel management systems available today, ultimately that extra time and knowledge can help prevent costly mistakes in the future.
Below is a guide to 10 questions to ask when purchasing a system, as well as important factors that you may want to consider. Let’s get started!
1) What features are exclusive to this system?
At first glance, all fuel management systems will likely appear very similar. In fact, you may not notice any strong differentiators right away. This is where the extra time and research we discussed earlier comes into play. No two systems are exactly the same once you dig down into the specific facts and features of each product. While you explore your options, identify those relevant features, noting any innovative benefits that might be oriented or customizable for the specifics of your business.
For example, thanks to new developments in technology, it’s now noticeably easier to track and generate reports required by state for applications for rebates related to off-road taxes. In the past, this feature didn’t exist in most systems.
2) Can it save our organization money?
Correct tracking and control of fuel spend are what can save organizations money. It reduces or eliminates theft and improper use, as well as it provides the ability to get accurate data that supports fleet maintenance and budgetary decisions.
No fuel management system is an ATM, but a good one will allow a fleet manager to eliminate errors while also identifying areas for potential savings.
In addition, a good system can cut down on personnel costs.
3) What new technology does this system offer?
More often than not, people assume that a new system will just replace their existing one and that everything will operate as it has in the past. They’re
4) What kind of customer support is offered?
When you’re in the market for a fuel management system, this is the single-most important factor to consider.
Furthermore, it’s helpful to have a service agreement policy and any relevant procedures in writing from the provider. Most fuel management system providers should issue that without a problem. If a provider doesn’t or won’t, that’s a signal to a potentially large problem. Be sure to discuss with the representative what the availability and success rates of their customer support department are. Understanding their level of commitment to you is important.
often surprised to discover a variety of new solution-centric technologies are now available to rectify common issues that arise in fuel management systems.
For example, real-time tools and powerful tracking features can provide information instantaneously that can help eliminate security flaws, identify mechanical problems, regulate fuel usage, facilitate accurate data collection and transmittal and more. All these tools and features save time to help reduce overall costs.
5) How will this affect my fuel audit process?
When it comes to fuel auditing, you should always be on the lookout for upgrades that can save time. Specifically, the upgrade must improve overall efficiency by reporting accurate data. Ideally, this workflow would interface with the tank level system and easily show fuel drops and transaction usage.
6) What is the system’s reliability?
A system and its software have to operate dependably, always. If they fail, it’s not only stressful but also risky, especially if the fuel is used by emergency vehicles.
Most systems should be able to operate consistently for 10 years or so before a large revamp deserves consideration. Often times, upgrades and replacement parts can extend the life of a dependable system to 15 or even 20 years. If it has a history of misuse or malfunction, be very wary.
Be sure to ask about cost and quality of installation as well.
7) How does the system improve fuel and data security?
When researching your options, you should look for a solution that prevents people from tricking the system and stealing from your organization, while also reducing or eliminating the potential for human error. Also, you should want easy-to-use tools that collect and deliver accurate data, so you can quickly determine whether an issue is related to compromised security or malfunctioning equipment or vehicles.
In your research, you’ll likely discover that providers are understanding the importance of a secure, accurate system more. As a result, many are developing advanced technologies and electronic gadgets designed to allow for less input from the user and reduce human interaction with the system.
8) Will this new system interface with my existing software?
These days, it seems like if an organization isn’t struggling with the mechanical parts of a piece of equipment, then it has issues with the software. If you spend the time to learn how the fuel management system’s software interacts with your internal software, you can save on a lot of headaches down the line.
9) What’s “green” about the system?
“Green” has a lot of meanings nowadays. It might relate to tracking fueling processes accurately and, consequently, reducing idling time or identifying emissions issues. It could also indicate a dispensing system that supports any number of fuels, including alternative options. At the same time, the possibility to operate those systems using solar or other alternative energy technologies can help promote an eco-positive attitude.
10) What is the ability of the system to upgrade?
Surprisingly, this is a topic that most buyers forget about during the researching and purchasing processes. However, understanding what the provider’s record has been in offering and implementing new equipment that’s backwards compatible is critical. A system that can be upgraded indicates that innovative developments can be incorporated into the existing system without requiring a new one, leading to cost savings as technologies change.